QIBR bearings are used in the magnetic bearing system of Swiss high-end machine tool spindles
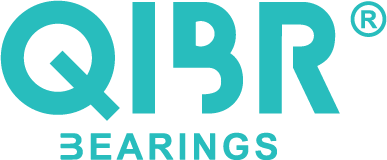
- Industry
- high-end machine tool manufacturing
- Location
- Switzerland
- Goals
- minimize downtime rate, improve equipment operation stability
Products used
QIBR bearings are used in the magnetic bearing system of Swiss high-end machine tool spindles
By limiting the rotor and providing temporary support when the magnetic bearing fails, the damage caused by the rotor falling can be reduced
Customer Introduction
Swiss High-end Machine Tool Factory is an internationally renowned company specializing in the manufacture of high-end CNC machine tools. Its products are widely used in aerospace, automobile manufacturing, precision machinery and other fields. With the continuous advancement of technology, customers have put forward higher requirements for the accuracy, speed and reliability of machine tool spindles.
a) Challenges (existing problems, why they have not been solved)
The main problem faced by current machine tool spindles when increasing speed and power is the complex dynamic response of the rotor falling and its thermal effect, which makes the protective shaft unable to play an effective protective role. The protective bearing is in a stationary state most of the time, has a short working time, and there is a small gap (0.1-0.5 mm) between it and the rotor, making it difficult to stably support complex load conditions and instantaneous impact forces.
Especially when the speed of a 4.5-ton vertical rotor reaches 10,000 rpm, the moment of inertia is 313.4 kg.m2, the energy storage is 172 MJ, and the equivalent friction coefficient of the bearing is 0.01, which makes the high rotor energy storage have the characteristics of high speed and large inertia. High-speed rotors work under vacuum conditions, with strict lubrication requirements, and when they fall, the heating and heat dissipation problems of the protective bearing are aggravated, limiting its reliability in the magnetic bearing system.
Therefore, the reliability of the protective bearing has become one of the main bottlenecks for increasing the speed and power of the current machine tool spindle.
b) Solution (How QIBR solves the problem)
QIBR's technical department adopted a multi-level simulation and experimental method to solve this problem. First, the contact model, dynamic model and thermal model of the protective bearing were established, and these models were coupled to comprehensively consider the thermal expansion characteristics of the material and the viscosity-temperature effect of the lubricant under high temperature vacuum conditions.
Secondly, the MATLAB simulation software was used to simulate the drop of the rotor at 5000 r/min and 20000 r/min, and the fourth-order Runge-Kutta method was used to solve the rotor axial displacement, rotor radial axis trajectory, protective bearing axial contact force, protective bearing radial contact force, speed change curve, temperature and wear change curve, etc. At the same time, the finite element analysis software was used to solve the first-order bending critical speed of 100130 r/min and the second-order bending critical speed of 192000 r/min. The simulation results provide data support for the research and development process and guide the selection of raw materials, cutting, stamping and forging processes.
After rigorous drop tests, the rotor axis trajectory, contact force, friction, wear and heating status of the protective bearing were monitored, and the experimental results were compared with the simulation data to verify the accuracy of the model and the effectiveness of the simulation. Finally, QIBR successfully developed the QIBR deep groove ball bearing as the protective bearing of the magnetic bearing system in the machine tool spindle.
c)Results
- Optimized the reliability of deep groove ball bearing protection when the rotor falls.
- Improved the stability and safety of the machine tool spindle system.
- Reduce equipment downtime caused by rotor falling.
- Improved the high temperature resistance and wear resistance of protected bearings.
- Reduces maintenance costs and equipment operation risks.
Customer testimonials
QIBR's technical experts provided us with efficient solutions. They improved and optimized the problem of the rotor being unable to float stably or falling due to electrical system failure or external impact during the application of the machine tool spindle, improving the reliability of the protective bearings. It reduces the losses caused by the rotor falling, improves the stability of the magnetic bearing system, and significantly improves the stability and reliability of our equipment. Through their products and services, we have successfully reduced downtime and increased productivity.
End customers have spoken highly of the QIBR deep groove ball bearings provided by QIBR, and we will continue to choose QIBR's professional products.
End customers have spoken highly of the QIBR deep groove ball bearings provided by QIBR, and we will continue to choose QIBR's professional products.