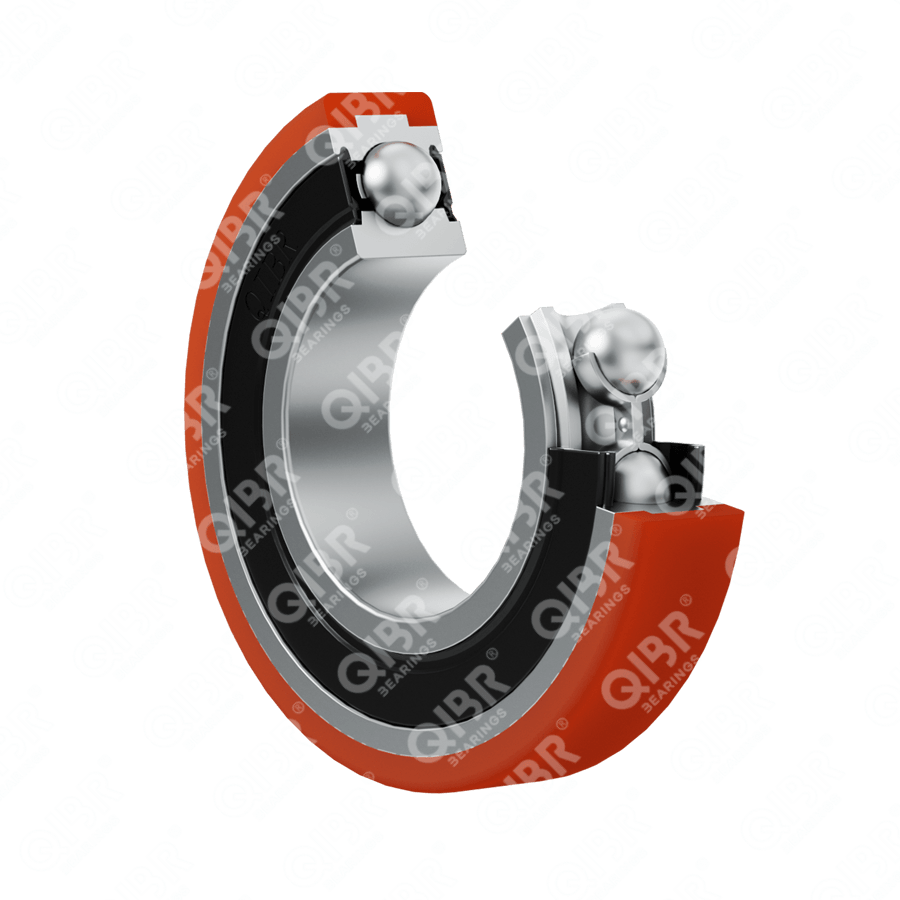
Image may differ from product. See technical specification for details.
Search for the bearing model you need
Standard
GB,ASTM/AISI,ГОСТ,BS,JIS,NF,DIN/VDEh,DIN/VDEh
Inner diameter
1.5mm-25mm
Outer diameter
7mm-80mm
Width
3mm-36mm
Dynamic radial load
2lbf-1888lbf
Coated material
NDI/POM Polyurethane
Static load rating,radial
1lbf-1059lbf
MAX speed
7.8-78 (X1000 rpm)
Brand
QIBR/OEM/Neutral
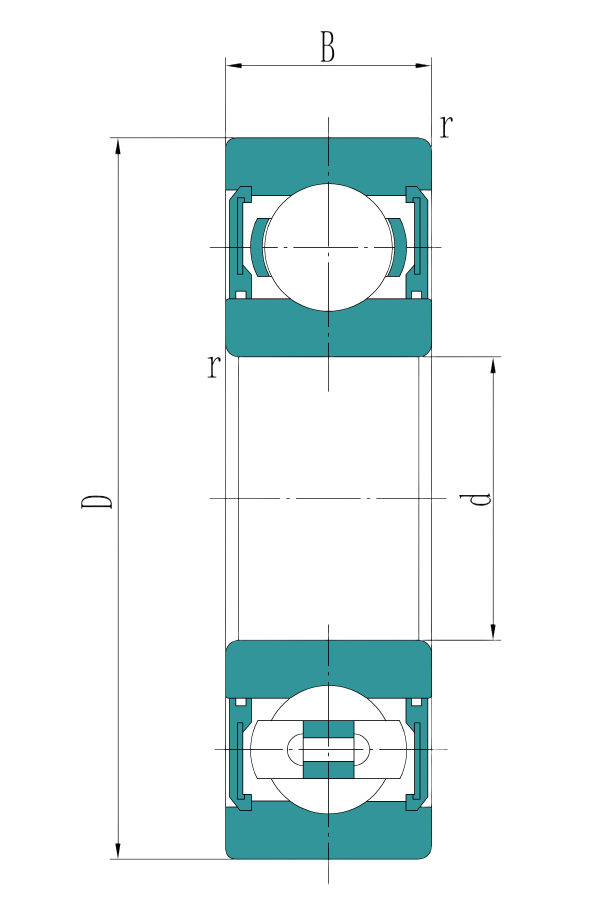
NO. | Product | Product Number | Bore | Inner ring type | Outer diameter (D) | Seal type | Shield material | Width |
---|---|---|---|---|---|---|---|---|
1 |
![]() |
6817 2rs | 1.5 mm | Normal | 7 mm | Sealed | NBR | 4 mm |
2 |
![]() |
6818 2rs | 1.5 mm | Normal | 8 mm | Sealed | NBR | 4 mm |
3 |
![]() |
6203 2rs | 17 mm | Normal | 50 mm | Sealed | NBR | 18 mm |
4 |
![]() |
6203 2rs | 17 mm | Normal | 60 mm | Sealed | NBR | 18 mm |
5 |
![]() |
6903 2rs | 17 mm | Normal | 40 mm | Sealed | NBR | 10 mm |
6 |
![]() |
683 2rs | 3mm | Normal | 10 mm | Sealed | NBR | 3 mm |
7 |
![]() |
683 2rs | 3 mm | Normal | 12 mm | Sealed | NBR | 3 mm |
8 |
![]() |
693 2rs | 3 mm | Normal | 10 mm | Sealed | NBR | 4 mm |
9 |
![]() |
693 2rs | 3 mm | Normal | 10 mm | Sealed | NBR | 5 mm |
10 |
![]() |
693 2rs | 3 mm | Normal | 12 mm | Sealed | NBR | 4 mm |
11 |
![]() |
604 2rs | 4 mm | Normal | 16 mm | Sealed | NBR | 5 mm |
12 |
![]() |
624 2rs | 4 mm | Normal | 15 mm | Sealed | NBR | 5 mm |
13 |
![]() |
624 2rs | 4 mm | Normal | 18 mm | Sealed | NBR | 5 mm |
14 |
![]() |
624 2rs | 4 mm | Normal | 30 mm | Sealed | NBR | 5 mm |
15 |
![]() |
684 2rs | 4 mm | Normal | 11 mm | Sealed | NBR | 4 mm |
16 |
![]() |
684 2rs | 4 mm | Normal | 12 mm | Sealed | NBR | 4 mm |
17 |
![]() |
684 2rs | 4 mm | Normal | 12 mm | Sealed | NBR | 6 mm |
18 |
![]() |
684 2rs | 4 mm | Normal | 13 mm | Sealed | NBR | 4 mm |
19 |
![]() |
684 2rs | 4 mm | Normal | 13 mm | Sealed | NBR | 8 mm |
20 |
![]() |
684 2rs | 4 mm | Normal | 14 mm | Sealed | NBR | 6 mm |
21 |
![]() |
605 2rs | 5 mm | Normal | 18 mm | Sealed | NBR | 5 mm |
22 |
![]() |
605 2rs | 5 mm | Normal | 19 mm | Sealed | NBR | 7 mm |
23 |
![]() |
605 2rs | 5 mm | Normal | 21 mm | Sealed | NBR | 8 mm |
24 |
![]() |
625 2rs | 5 mm | Normal | 20 mm | Sealed | NBR | 5 mm |
25 |
![]() |
625 2rs | 5 mm | Normal | 22 mm | Sealed | NBR | 5 mm |
26 |
![]() |
625 2rs | 5 mm | Normal | 22 mm | Sealed | NBR | 7 mm |
27 |
![]() |
625 2rs | 5 mm | Normal | 22 mm | Sealed | NBR | 9 mm |
28 |
![]() |
625 2rs | 5 mm | Normal | 24 mm | Sealed | NBR | 5 mm |
29 |
![]() |
625 2rs | 5 mm | Normal | 25 mm | Sealed | NBR | 9 mm |
30 |
![]() |
685 2rs | 5 mm | Normal | 16 mm | Sealed | NBR | 5 mm |
31 |
![]() |
685 2rs | 5 mm | Normal | 16 mm | Sealed | NBR | 8 mm |
32 |
![]() |
685 2rs | 5 mm | Normal | 17 mm | Sealed | NBR | 10 mm |
33 |
![]() |
695 2rs | 5 mm | Normal | 18 mm | Sealed | NBR | 5 mm |
34 |
![]() |
606 2rs | 6 mm | Normal | 21 mm | Sealed | NBR | 9 mm |
35 |
![]() |
606 2rs | 6 mm | Normal | 22 mm | Sealed | NBR | 6 mm |
36 |
![]() |
606 2rs | 6 mm | Normal | 24 mm | Sealed | NBR | 6 mm |
37 |
![]() |
626 2rs | 6 mm | Normal | 24 mm | Sealed | NBR | 24 mm |
38 |
![]() |
626 2rs | 6 mm | Normal | 25 mm | Sealed | NBR | 18 mm |
39 |
![]() |
626 2rs | 6 mm | Normal | 26 mm | Sealed | NBR | 10 mm |
40 |
![]() |
626 2rs | 6 mm | Normal | 26 mm | Sealed | NBR | 12 mm |
41 |
![]() |
626 2rs | 6 mm | Normal | 26 mm | Sealed | NBR | 8 mm |
42 |
![]() |
626 2rs | 6 mm | Normal | 28 mm | Sealed | NBR | 13 mm |
43 |
![]() |
626 2rs | 6 mm | Normal | 28 mm | Sealed | NBR | 6 mm |
44 |
![]() |
626 2rs | 6 mm | Normal | 30 mm | Sealed | NBR | 10 mm |
45 |
![]() |
626 2rs | 6 mm | Normal | 30 mm | Sealed | NBR | 12 mm |
46 |
![]() |
626 2rs | 6 mm | Normal | 30 mm | Sealed | NBR | 9 mm |
47 |
![]() |
626 2rs | 6 mm | Normal | 33 mm | Sealed | NBR | 7 mm |
48 |
![]() |
626 2rs | 6 mm | Normal | 35 mm | Sealed | NBR | 14 mm |
49 |
![]() |
626 2rs | 6 mm | Normal | 40 mm | Sealed | NBR | 10 mm |
50 |
![]() |
696 2rs | 6 mm | Normal | 18 mm | Sealed | NBR | 7 mm |
51 |
![]() |
696 2rs | 6 mm | Normal | 19 mm | Sealed | NBR | 5 mm |
52 |
![]() |
696 2rs | 6 mm | Normal | 20 mm | Sealed | NBR | 5 mm |
53 |
![]() |
696 2rs | 6 mm | Normal | 20 mm | Sealed | NBR | 6 mm |
54 |
![]() |
696 2rs | 6 mm | Normal | 20 mm | Sealed | NBR | 8 mm |
55 |
![]() |
696 2rs | 6 mm | Normal | 22 mm | Sealed | NBR | 5 mm |
56 |
![]() |
696 2rs | 6 mm | Normal | 22 mm | Sealed | NBR | 7 mm |
57 |
![]() |
608 2rs | 8 mm | Normal | 24 mm | Sealed | NBR | 7 mm |
58 |
![]() |
608 2rs | 8 mm | Normal | 26 mm | Sealed | NBR | 7 mm |
59 |
![]() |
608 2rs | 8 mm | Normal | 28 mm | Sealed | NBR | 10 mm |
60 |
![]() |
608 2rs | 8 mm | Normal | 28 mm | Sealed | NBR | 7 mm |
61 |
![]() |
608 2rs | 8 mm | Normal | 28 mm | Sealed | NBR | 8 mm |
62 |
![]() |
608 2rs | 8 mm | Normal | 30 mm | Sealed | NBR | 11 mm |
63 |
![]() |
608 2rs | 8 mm | Normal | 30 mm | Sealed | NBR | 7 mm |
64 |
![]() |
608 2rs | 8 mm | Normal | 30 mm | Sealed | NBR | 9 mm |
65 |
![]() |
608 2rs | 8 mm | Normal | 32 mm | Sealed | NBR | 10 mm |
66 |
![]() |
608 2rs | 8 mm | Normal | 32 mm | Sealed | NBR | 12 mm |
67 |
![]() |
608 2rs | 8 mm | Normal | 35 mm | Sealed | NBR | 12 mm |
68 |
![]() |
608 2rs | 8 mm | Normal | 35 mm | Sealed | NBR | 15 mm |
69 |
![]() |
608 2rs | 8 mm | Normal | 35 mm | Sealed | NBR | 18 mm |
70 |
![]() |
608 2rs | 8 mm | Normal | 36 mm | Sealed | NBR | 10 mm |
71 |
![]() |
608 2rs | 8 mm | Normal | 40 mm | Sealed | NBR | 11 mm |
72 |
![]() |
608 2rs | 8 mm | Normal | 40 mm | Sealed | NBR | 13 mm |
73 |
![]() |
608 2rs | 8 mm | Normal | 45 mm | Sealed | NBR | 14 mm |
74 |
![]() |
608 2rs | 8 mm | Normal | 48 mm | Sealed | NBR | 16 mm |
75 |
![]() |
628 2rs | 8 mm | Normal | 45 mm | Sealed | NBR | 8 mm |
76 |
![]() |
638 2rs | 8 mm | Normal | 40 mm | Sealed | NBR | 20 mm |
77 |
![]() |
638 2rs | 8 mm | Normal | 45 mm | Sealed | NBR | 20 mm |
78 |
![]() |
688 2rs | 8 mm | Normal | 22 mm | Sealed | NBR | 5 mm |
79 |
![]() |
688 2rs | 8 mm | Normal | 22 mm | Sealed | NBR | 7 mm |
80 |
![]() |
6000 2rs | 10 mm | Normal | 30 mm | Sealed | NBR | 11 mm |
81 |
![]() |
6000 2rs | 10 mm | Normal | 32 mm | Sealed | NBR | 10 mm |
82 |
![]() |
6000 2rs | 10 mm | Normal | 34 mm | Sealed | NBR | 11 mm |
83 |
![]() |
6000 2rs | 10 mm | Normal | 35 mm | Sealed | NBR | 11 mm |
84 |
![]() |
6000 2rs | 10 mm | Normal | 38 mm | Sealed | NBR | 10 mm |
85 |
![]() |
6000 2rs | 10 mm | Normal | 40 mm | Sealed | NBR | 10 mm |
86 |
![]() |
6200 2rs | 10 mm | Normal | 36 mm | Sealed | NBR | 13 mm |
87 |
![]() |
6200 2rs | 10 mm | Normal | 36 mm | Sealed | NBR | 16 mm |
88 |
![]() |
6200 2rs | 10 mm | Normal | 40 mm | Sealed | NBR | 11 mm |
89 |
![]() |
6200 2rs | 10 mm | Normal | 40 mm | Sealed | NBR | 12 mm |
90 |
![]() |
6200 2rs | 10 mm | Normal | 50 mm | Sealed | NBR | 12 mm |
91 |
![]() |
6200 2rs | 10 mm | Normal | 60 mm | Sealed | NBR | 12 mm |
92 |
![]() |
6900 2rs | 10 mm | Normal | 25.4 mm | Sealed | NBR | 7 mm |
93 |
![]() |
6900 2rs | 10 mm | Normal | 26 mm | Sealed | NBR | 10 mm |
94 |
![]() |
6001 2rs | 12 mm | Normal | 40 mm | Sealed | NBR | 13 mm |
95 |
![]() |
6001 2rs | 12 mm | Normal | 45 mm | Sealed | NBR | 14 mm |
96 |
![]() |
6201 2rs | 12 mm | Normal | 38 mm | Sealed | NBR | 10 mm |
97 |
![]() |
6201 2rs | 12 mm | Normal | 40 mm | Sealed | NBR | 18 mm |
98 |
![]() |
6201 2rs | 12 mm | Normal | 50 mm | Sealed | NBR | 20 mm |
99 |
![]() |
6901 2rs | 12 mm | Normal | 28 mm | Sealed | NBR | 8 mm |
100 |
![]() |
6901 2rs | 15 mm | Normal | 40 mm | Sealed | NBR | 12 mm |
Features and advantages of QIBR polyurethane coated bearing
The QIBR polyurethane coated bearing solves several key issues across various fields, mainly reflected in the following aspects:
1. Wear resistance
The QIBR polyurethane coated bearing has excellent wear resistance, which reduces wear over long-term operation and extends its service life, especially suitable for high-load or high-friction environments.
2. Shock absorption and noise reduction
The QIBR polyurethane coated bearing has good elasticity and buffering properties, effectively absorbing vibrations and reducing noise.
3. Oil and chemical corrosion resistance
The QIBR polyurethane coated bearing has good resistance to oils, solvents, and various chemicals.
4. Impact resistance
The high elasticity of the QIBR polyurethane coated bearing gives it good impact resistance, making it suitable for environments with impact loads.
Performance improvements and solutions for QIBR polyurethane coated bearing
1. Enhanced wear resistance
By adding reinforcing materials such as carbon black, ceramics, and metal powders, the hardness and wear resistance of polyurethane can be improved, enabling it to maintain stable performance under higher loads and long-term use.
2. Improved oil and chemical resistance
Depending on the bearing’s operating environment, polyurethane formulas with stronger chemical corrosion and oil resistance can be selected, improving the bearing's lifespan in chemical and oil-contaminated environments.
3. Optimization of polyurethane layer thickness
The thickness of the polyurethane layer directly affects the performance of the outsourcing polyurethane bearing. An appropriate thickness can improve the bearing's impact resistance and wear resistance. However, too thick a polyurethane layer may reduce the bearing's rigidity and affect performance. A reasonable design of the polyurethane layer thickness can meet the requirements for shock absorption and wear resistance while maintaining the bearing's load capacity and operational stability.
4. Inner and outer ring structure optimization
By optimizing the geometric shapes and dimensions of the inner and outer rings, the polyurethane layer can be evenly stressed, preventing local over-wear.
Main application areas of QIBR polyurethane coated bearing
1. Automotive industry
Polyurethane bearings are widely used in the automotive industry, especially in suspension systems, drive systems, and brake systems. Due to the polyurethane material's ability to absorb vibrations, reduce noise, and provide strong durability, it is used in: automotive wheel axles and suspension systems, engine and transmission components, wheels, and brake systems.
2. Mechanical engineering
In mechanical engineering, polyurethane bearings are used in various mechanical equipment requiring wear resistance and high load capacity. Their elasticity and toughness enable them to operate under heavy loads and high-impact conditions.
3. Sports equipment
Polyurethane bearings are commonly used in various sports equipment and tools, especially in components that require wear resistance and impact resistance. These include: skateboards, skis, rollerblades, and other sporting goods.
4. Aerospace
In the aerospace industry, polyurethane bearings are used in some aircraft components due to their excellent high-temperature and wear-resistant properties. They can withstand high-speed operation and extreme environmental loads.
5. Robotics and automation
Polyurethane bearings are also widely used in robotics and automation equipment. They can reduce friction and noise while ensuring high-precision and high-speed motion, thus extending the service life of the equipment.