QIBR double-row tapered bearings are used in high-speed train axle boxes
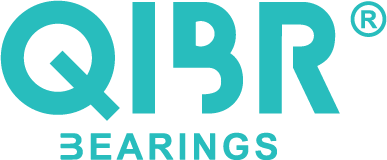
- Industry
- High-speed rail industry
- Location
- Germany
- Goals
- Reduce friction heat generated during operation and improve equipment operation stability
Products used
QIBR double-row tapered bearings are used in high-speed train axle boxes
-Improve train operation stability by reducing the friction heat generated during bearing operation
At the 2018 Shanghai Bauma Exhibition, a German high-speed train manufacturer approached us, seeking solutions to ensure stable railway operations under harsh conditions. We quickly assembled a team of experts to thoroughly analyze the challenges faced by the client. After months of repeated discussions and trials, we continuously adjusted and optimized our solutions to achieve the best results. Each prototype underwent rigorous testing to ensure it could withstand extreme environmental conditions in real-world applications. Eventually, we successfully provided the client with a comprehensive solution, completely resolving their issues with railway stability under adverse conditions. The client highly appreciated our professional capabilities and problem-solving efficiency, expressing a desire for more collaboration opportunities in the future.
Here are the details of this case,
1. Challenges
The bogie of a high-speed train is one of the most important components in the structure of a rail vehicle, and its parameters directly affect the stability and ride comfort of the vehicle. As an important mechanical operating component of the bogie, the axle box bearing is often subjected to an instantaneous alternating load. Due to the serpentine motion of the rail vehicle, the contact state of the roller of the axle box bearing relative to the raceway is unstable under the action of the instantaneous alternating load, which can easily lead to the destruction of the lubricating oil film, thereby causing wear and material peeling, which has a great impact on the operation of the train.
In order to change the adverse factors of bearings on trains, high-speed railway technicians have statistically analyzed the maintenance data of different bearings: a total of 7,314 sets of double-row cylindrical axle box bearings were overhauled, 5,623 sets were repaired, and the repair rate was 77%. 12,245 sets of double-row tapered axle box bearings were overhauled, 11,675 sets were repaired, and the repair rate was 95%. Relatively speaking, double-row tapered bearings are more suitable for high-speed train operating conditions.
However, in hot summer or under special road conditions, the friction between the ribs and roller end faces of double-row tapered bearings generates a lot of friction heat, which causes high-temperature alarms in the axle box bearings, thus affecting the operating efficiency and reliability of the high-speed rail line. Therefore, how to ensure the stable operation of the axle box bearings under harsh working conditions such as high speed, heavy load, high temperature, large temperature difference and high vibration and shock has become an important challenge that double-row tapered bearings need to face.
2. Solutions
QIBR worked closely with the client company to obtain detailed data. In response to the problems of existing double-row tapered bearings, QIBR technicians made a series of improvements, mainly including the following aspects:
1) Data analysis and improvement: Through the data analysis provided by the cooperative company, QIBR technicians found that the traditional double-row tapered bearings had a total of 7,314 sets of bearings overhauled and 5,623 sets repaired. The repair rate at a high-speed train speed of 400km/h was 95%, and there was a record of high-temperature alarm. Therefore, QIBR improved the double-row tapered bearings and designed the QIBR series double-row tapered bearings to reduce friction and heat generation.
2) Bearing materials and processes: For high-speed trains, in order to ensure its performance and safety during high-speed operation, high-carbon chromium bearing steel is selected for the inner ring, outer ring and rollers, and the surface is carburized, nitrided, chrome-plated and other treatments are performed to improve wear resistance and fatigue resistance. The cage uses carbon fiber reinforced composite materials with higher strength and temperature resistance. Among them, the bearing accuracy reaches P4 level, which plays a vital role in the smooth operation of the train.
3) Lubricant replacement: The original 40°C corresponding to the base oil viscosity of 82mm²/s lubricant was replaced with a low friction grease with a base oil viscosity of 42mm²/s to reduce friction heating.
4) Bearing parameter optimization: A bearing-vehicle-track coupling dynamics model was established. In the equivalent bearing model, a No. 2 hinge connection was used between the bearing mass and the axle. The No. 43 force element in the Simpack software was used to simulate the equivalent stiffness of the bearing, and the stiffness value was calculated by the BearingX software. The calculated radial stiffness, axial stiffness, and angular stiffness were 6997.6MN/m, 602.6MN/m, and 24797304.0N.m/rad, respectively.
5) Temperature detection and testing: A temperature detection point was set near the outer ring of the bearing on the axle box housing. The test showed that the operating temperature of the double-row tapered axle box bearing designed by QIBR was about 15°C lower than the original design at a speed of 400km/h.
6) Thermal simulation analysis: A simplified model for thermal simulation analysis of the axle box system was established using CERO software, taking into account air convection heat dissipation during high-speed operation and extreme operating conditions in hot summer. The results showed that the maximum temperature of the axle box system designed by QIBR was approximately 20°C lower than that of the original design.
c) Results
i. The design of the bearings has been optimized to make them more stable at high speeds.
ii. The operating efficiency and reliability of high-speed trains have been improved.
iii. The frictional heating of the axlebox bearings has been reduced, making their performance more stable in high temperature environments.
iv. The lubricating grease has been improved to reduce friction loss and the risk of high temperature alarms.
v. The downtime of the equipment has been reduced, thereby improving overall profitability.
3. Customer Testimonials
“QIBR's technical experts provided us with QIBR double-row tapered bearings, which were optimized to solve the problems of large amounts of frictional heat generated in our equipment and instability under harsh working conditions. According to the test data of our company's technical department, when the speed reaches 400km/h, the frictional heat consumption of the double-row tapered axlebox bearing designed by QIBR is about 24% lower than that of the double-row tapered axlebox bearings used before. When the speed is increased, the operating temperature of the double-row tapered axlebox bearing designed by QIBR is about 15°C lower than that of the original double-row tapered axlebox bearings.
This shows that the QIBR double-row tapered bearings can operate stably under harsher working conditions. Through cooperation with QIBR, we have optimized the stability of the high-speed rail line. The end customers have given high praise to QIBR, and we will continue to choose QIBR's professional products.”
QIBR's technical experts provided us with QIBR double-row tapered bearings, which were optimized to solve the problems of large amounts of frictional heat generated in our equipment and instability under harsh working conditions.