QIBR double-row tapered roller bearings are used on railway freight cars
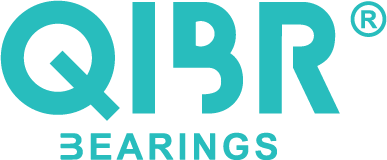
- Industry
- Rail Industry
- Location
- Brazil
- Goals
- By optimizing bearing materials and processes, the surface peeling damage rate of bearings is reduced.
Products used
QIBR double-row tapered roller bearings are used on railway freight cars
-By optimizing bearing materials and processes, the surface peeling damage rate of bearings is reduced
In 2021, a Brazilian engineering project company found us and hoped that we could help them provide a solution to reduce the surface peeling damage rate of tapered roller bearings. We quickly assembled an expert team to thoroughly analyze the challenges faced by the customer. After months of repeated discussions and trials, we continuously adjusted and optimized our solutions to achieve the best results. Each prototype has undergone strict testing to ensure that it can operate smoothly in actual use. Eventually, we successfully provided the customer with a comprehensive solution and successfully reduced the probability of tapered roller bearing damage. The customer highly appreciates our professional ability and problem-solving efficiency and expresses the hope for more cooperation opportunities in the future.
Here are the details of this case,
1. Challenges
The existing problems and why they haven't been solved: With the continuous increase in the running speed of railway trains and the increase in vehicle load, the problem of tapered roller bearing failure is becoming increasingly serious. According to data provided by partners, more than 2,000 sets of faulty bearings have been inspected, among which peeling is particularly prominent. This kind of peeling mostly occurs on the working surface where the bearing ring and roller cooperate, and is caused by contact fatigue.
The damage of mechanical parts generally starts from the surface layer. The texture structure of the part surface (such as surface roughness and shape error) and mechanical and physical properties (such as residual stress and hardness) are extremely important. Residual stress is an important parameter characterizing the quality of the processed metamorphic layer and surface layer, and has a decisive influence on the service performance and fatigue strength of parts. Therefore, it is very important to change the residual stress and thereby reduce the damage of the bearing due to surface peeling.
2. Solutions
QIBR technical team conducted in-depth analysis on the damaged bearing samples provided by customers and comprehensively optimized the traditional double-row tapered roller bearings. Specific measures include:
1) Bearing materials and processes: The outer and inner rings of the bearing are made of G20CrNi2MoA carburized bearing steel. After carburizing, quenching and tempering heat treatment processes, the effective wall thickness of the finished ring is 14mm to 20mm; the rollers are made of GCr15 high-carbon bearing steel and go through quenching and tempering treatment.
2) Heat treatment optimization: Perform carburizing, primary and secondary quenching and tempering treatment on the bearing ring. By adjusting the carbon potential, temperature, furnace pressure and the cooling performance of the quenching medium, an ideal surface compressive stress is obtained.
3) Grinding process: In the initial grinding stage, the grinding allowance and heat treatment metamorphic layer are removed, and a coarse-grained grinding wheel is used. In the final grinding stage, a fine-grained, small-pore, high-hardness grinding wheel is selected, and the grinding speed and workpiece rotation speed are finely adjusted to ensure the normal operation of the cooling system, reduce grinding stress and increase surface compressive stress.
4) Superfinishing technology: Adopt composite superfinishing and reticulated superfinishing technology to improve the surface accuracy of the raceway, improve the lubrication state and form a uniform compressive stress. The number of oilstone meshes for superfinishing the ring is 800# - 1200#, and aviation kerosene is used as the grinding fluid.
5) Production process: Starting from the incoming inspection of raw materials, including forging, rolling and forming, turning processing, carburizing and heat treatment (primary quenching, tempering, secondary quenching, tempering), sandblasting or shot blasting, initial grinding (including plane, outer diameter, inner ring raceway, etc.), additional tempering, ultrasonic flaw detection, final grinding (including superfinishing), magnetic particle inspection, final inspection, phosphating, to bearing assembly.
c) Results
i. Optimized bearing materials and process flow, improving the overall durability and performance stability of the product.
ii. Enhanced the fatigue strength and peeling resistance of the bearing, prolonging the service life.
iii. Reduced equipment downtime due to bearing failure and improved the operating efficiency of the train.
iv. Improved the surface quality and processing accuracy of the bearing and improved the working state of the bearing.
v. Reduced maintenance costs and equipment failure rates, significantly improving the profitability of customers.
3. Customer Testimonials
QIBR technical experts analyzed the bearing surface peeling phenomenon and provided us with targeted products and solutions. Through the optimization of bearing materials and processes, the bearing failure problem encountered during high-speed and heavy-load operation was solved. The surface damage problem of bearings caused by contact fatigue was greatly reduced. After installing QIBR double-row tapered roller bearings, the freight car runs more smoothly.
After a long time of data feedback, using the improved QIBR double-row tapered roller bearings prolongs the service life of freight cars and reduces maintenance costs. Cooperation with QIBR is very pleasant and meets our expectations. We will continue to choose QIBR's professional products.
QIBR technical experts analyzed the bearing surface peeling phenomenon and provided us with targeted products and solutions.