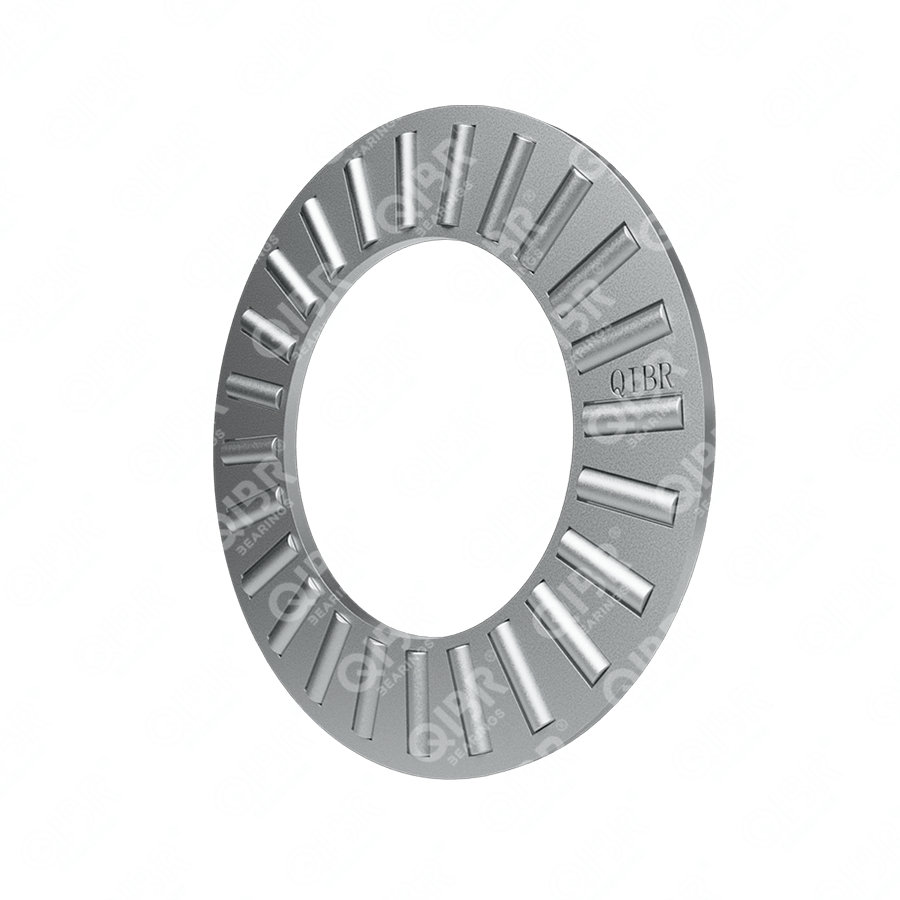
Image may differ from product. See technical specification for details.
Search for the bearing model you need
Standard
GB,ASTM/AISI,ГОСТ,BS,JIS,NF,DIN / VDEh
Material
52100/100Cr6/SUJ2/Stainless Steel
Brand
QIBR/OEM/Neutral
Package
QIBR/Standard Industrial Package/OEM
Package
QIBR/Standard Industrial Package/OEM
Outer diameter (D)
14-200mm
Applications
This type of bearing is suitable for situations where the shaft and seat hole can be used as raceways
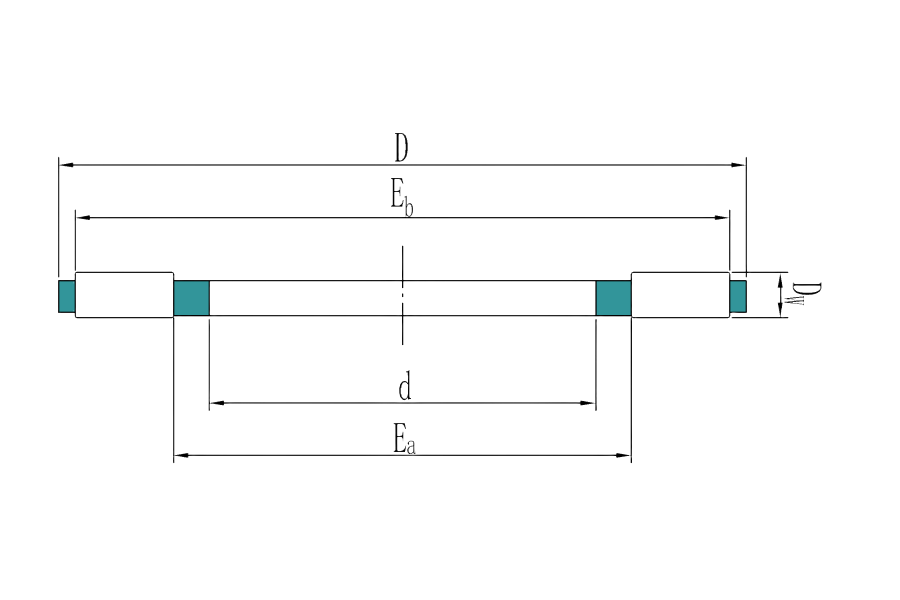
NO. | Product | Product Number | Basic dynamic load rating | Basic static load rating | Bore | Diameter roller (Dw) | Limiting speed | Outer diameter (D) |
---|---|---|---|---|---|---|---|---|
1 |
![]() |
AXK 0414 TN | 4.15 KN | 8.3 KN | 4 mm | 2 mm | 15000 rpm | 14 mm |
2 |
![]() |
AXK 0515 TN | 4.5 KN | 9.5 KN | 5 mm | 2 mm | 14000 rpm | 15 mm |
3 |
![]() |
AXK 0619 TN | 6.3 KN | 16 KN | 6 mm | 2 mm | 12000 rpm | 19 mm |
4 |
![]() |
AXK 0821 TN | 7.2 KN | 20 KN | 8 mm | 2 mm | 11000 rpm | 21 mm |
5 |
![]() |
AXK 1024 | 8.5 KN | 26 KN | 10 mm | 2 mm | 10000 rpm | 24 mm |
6 |
![]() |
AXK 1226 | 9.15 KN | 30 KN | 12 mm | 2 mm | 10000 rpm | 26 mm |
7 |
![]() |
AXK 1528 | 10.4 KN | 37.5 KN | 15 mm | 2 mm | 9500 rpm | 28 mm |
8 |
![]() |
AXK 1730 | 11 KN | 40.5 KN | 17 mm | 2 mm | 9500 rpm | 30 mm |
9 |
![]() |
AXK 2035 | 12 KN | 47.5 KN | 20 mm | 2 mm | 8500 rpm | 35 mm |
10 |
![]() |
AXK 2542 | 13.4 KN | 60 KN | 25 mm | 2 mm | 7500 rpm | 42 mm |
11 |
![]() |
AXK 3047 | 15 KN | 72 KN | 30 mm | 2 mm | 7000 rpm | 47 mm |
12 |
![]() |
AXK 3552 | 16.6 KN | 83 KN | 35 mm | 2 mm | 6300 rpm | 52 mm |
13 |
![]() |
AXK 4060 | 25 KN | 114 KN | 40 mm | 3 mm | 5600 rpm | 60 mm |
14 |
![]() |
AXK 4565 | 27 KN | 127 KN | 45 mm | 3 mm | 5300 rpm | 65 mm |
15 |
![]() |
AXK 5070 | 28.5 KN | 143 KN | 50 mm | 3 mm | 5000 rpm | 70 mm |
16 |
![]() |
AXK 5578 | 34.5 KN | 186 KN | 55 mm | 3 mm | 4300 rpm | 78 mm |
17 |
![]() |
AXK 6085 | 37.5 KN | 232 KN | 60 mm | 3 mm | 4300 rpm | 85 mm |
18 |
![]() |
AXK 6590 | 39 KN | 255 KN | 65 mm | 3 mm | 4000 rpm | 90 mm |
19 |
![]() |
AXK 7095 | 49 KN | 255 KN | 70 mm | 4 mm | 3600 rpm | 95 mm |
20 |
![]() |
AXK 75100 | 50 KN | 265 KN | 75 mm | 4 mm | 3400 rpm | 100 mm |
21 |
![]() |
AXK 80105 | 51 KN | 280 KN | 80 mm | 4 mm | 3400 rpm | 105 mm |
22 |
![]() |
AXK 85110 | 52 KN | 290 KN | 85 mm | 4 mm | 3400 rpm | 110 mm |
23 |
![]() |
AXK 90120 | 65.5 KN | 405 KN | 90 mm | 4 mm | 3000 rpm | 120 mm |
24 |
![]() |
AXK 100135 | 76.5 KN | 560 KN | 100 mm | 4 mm | 2800 rpm | 135 mm |
25 |
![]() |
AXK 110145 | 81.5 KN | 620 KN | 110 mm | 4 mm | 2600 rpm | 145 mm |
26 |
![]() |
AXK 120155 | 86.5 KN | 680 KN | 120 mm | 4 mm | 2600 | 155 mm |
27 |
![]() |
AXK 130170 | 112 KN | 830 KN | 130 mm | 5 mm | 2200 rpm | 170 mm |
28 |
![]() |
AXK 140180 | 116 KN | 900 KN | 140 mm | 5 mm | 2000 rpm | 180 mm |
29 |
![]() |
AXK 150190 | 120 KN | 950 KN | 150 mm | 5 mm | 2000 rpm | 190 mm |
30 |
![]() |
AXK 160200 | 125 KN | 1000 KN | 160 mm | 5 mm | 1900 r/min | 200 mm |
QIBR needle roller-cage thrust assembly solves multiple key problems in various fields, which are mainly reflected in the following aspects:
1. Compact structure
Due to the use of needle rollers as rolling elements, the needle roller-cage thrust assembly is relatively small in size while carrying large axial loads, and can be installed in a limited space, which is particularly suitable for compact mechanical design.
2. Low friction and high efficiency
Due to the precision design between the needle roller and the cage, the needle roller-cage thrust assembly has lower friction loss, reduces heat generation, and improves working efficiency. This makes it suitable for high-speed and high-efficiency working environments.
3. Strong durability
The cage can maintain the stable position of the needle roller, reduce mutual contact and wear between the needle rollers, and thus extend the service life of the bearing. Reasonable clearance and precision design ensure the stability and reliability of the bearing in operation.
4. Low noise and vibration
Due to the reasonable structural design between the needle roller and the cage, the possibility of mutual contact between the needle rollers is reduced, and the noise and vibration of the bearing are reduced, so it is suitable for working environments requiring low noise.
5. Adapt to high speed
Due to the small shape of the needle roller and the small contact area, the needle roller-cage thrust assembly is suitable for high speed applications and is not prone to excessive friction or overheating due to excessive speed.
QIBR needle roller-cage thrust assembly performance improvement and solutions
1. Improved materials
Selection of high-performance materials: Using materials with higher hardness, wear resistance and corrosion resistance can significantly improve the durability and stability of bearings.
Surface treatment: Surface treatment of key components such as needle rollers and cages of bearings (such as nitriding, chrome plating, coating, etc.) can improve surface hardness and wear resistance, reduce friction and wear, and thus extend service life.
2. Optimize cage design
Cage structure optimization: Optimize the cage structure design to achieve better needle roller arrangement and uniform load distribution. Improving the cage structure can reduce the mutual collision of needle rollers and improve operating stability and efficiency.
Reduce contact area: By optimizing the geometry of the cage and the arrangement of needle rollers, the contact area between needle rollers is reduced, thereby reducing friction and wear.
3. Improve lubrication performance
High-efficiency lubricating materials: Use grease or lubricating oil that is more suitable for high temperature and high pressure environments to ensure that the lubricating oil can maintain stable performance under long-term work, thereby reducing bearing friction and improving durability.
4. Improve precision and tolerance control
Precision machining technology: By improving manufacturing accuracy, reducing the gap and error between bearing components, ensuring a more uniform and stable contact between the needle roller and the cage. This can not only improve the performance of the bearing, but also extend its service life and reduce noise and vibration.
Main application areas of QIBR needle roller-cage thrust assemblies
1. Automobile differentials
In differentials, needle roller-cage thrust assemblies are used to support components that bear axial forces to ensure that the car can run smoothly when turning.
2. Aircraft structure
Some rotating parts of aircraft, such as steering gear systems, also use needle roller-cage thrust assemblies to reduce structural weight and increase load-bearing capacity.
3. Hydraulic pumps and pneumatic valves
In hydraulic and pneumatic systems, needle roller-cage thrust assemblies are used to support and rotate components such as compressors, pumps or valves to ensure efficient operation of equipment.
4. Power tools
In the transmission system of power tools (such as electric drills, cutting machines, etc.), needle roller-cage thrust assemblies are used to bear large axial loads to ensure smooth and efficient operation of power tools.