QIBR deep groove ball bearings are used in traction motors
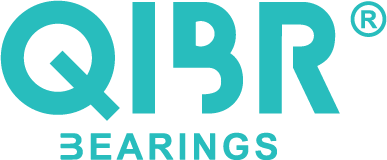
- Industry
- Railway Locomotive Industry
- Location
- Italy
- Goals
- reduced the surface damage rate of bearings
Products used
QIBR deep groove ball bearings are used in traction motors
By reducing the vibration value of bearings and optimizing grease, the surface damage rate of bearings is reduced
a) Challenges (existing problems and why they haven't been solved)
With the rapid development of heavy-load application of railway locomotives in China, the load and impact vibration borne by the traction motor bearings have increased significantly, which brings new challenges to the life reliability of motor bearings. During the service life of traction motor bearings, a large number of bearing fatigue failure faults have occurred.
QIBR technicians conducted detection and analysis on the damage of the outer raceway surface of the deep groove ball bearings provided by customers. The data shows that the damage of the outer raceway surface of deep groove ball bearings belongs to subsurface-origin fatigue spalling. The main reasons are related to factors such as alternating loads and poor lubrication in the use environment. According to Hertz theory, under the action of rolling contact load, the structure changes and microcracks begin to appear on the subsurface. These microcracks usually extend to the rolling contact surface, and then produce small flake spalling, point spalling, and then expand or form large-area spalling.
The damage of bearings will lead to the failure of the traction motor's operation, thus posing a major hidden danger to the safety of locomotive operation. How to avoid bearing damage is a great challenge for current traction motors.
b) Solution (How does QIBR solve the problem)
QIBR technicians analyzed the vibration data of the motor. The data shows that the measured vertical vibration is 3.56g, the standard value is 3.06g, and the foreign reference value is 1.70g. The measured lateral vibration is 6.47g, the standard value is 2.66g, and the foreign reference value is 0.16g. The measured longitudinal vibration is 3.71g, the standard value is 1.42g, and the foreign reference value is 0g. It can be seen from the data that the vibration effective values of the failed bearings in three directions are significantly greater than the standard values and foreign reference values. Among them, the measured value of lateral vibration is 2.5 times different from the standard value, which greatly increases the axial load of deep groove ball bearings and shortens the bearing life.
QIBR technicians analyze and adjust bearing vibration: 1. Improve bearing accuracy: QIBR provides bearings with an accuracy of P4 level to solve the bearing load problem. 2. Balance adjustment: Adjust the rotor balance. 3. Add monitoring equipment: Add vibration monitoring equipment to reflect the bearing operating status in real time. 4. Increase rigidity: Increase the rigidity of the bearing support structure and adjust the appropriate support structure and bearing housing geometry shape according to the design of the traction motor to reduce the impact on the bearings and unnecessary vibration.
The QIBR technical department inspected the grease in the peeled and unpeeled bearing samples provided by the customer. The results show that the content of iron and copper wear elements in the grease is on the high side, the grease hardens, and the oil separation rate increases. The grease appears black, hard, and dry.
From the inspection report, it is concluded that the implementation of the grease replenishment cycle fails to meet the grease replenishment requirements of the motor bearings under the actual operating conditions. To change this phenomenon, QIBR technicians optimize the bearing grease replenishment cycle, grease oil cycle, and grease type. The cycle of replenishing 240g of grease every 1 year or 20×10^4km of operation is optimized to replenishing 100g of grease every 3 months or 6×10^4km of operation. And for the operating conditions of heavy load and large vibration and impact of locomotives, use grease with stronger anti-wear and extreme pressure performance to increase the strength of the grease oil film and buffer and absorb bearing vibration. Excellent lubricating and flowing extreme pressure grease can increase the strength of the lubricating film and ensure effective lubrication of the bearings.
After implementing the optimization scheme, after 100×10^4km of operation, the motor bearings are in good condition. The obtained data shows that the optimization scheme effectively solves the fault problem of fatigue spalling of deep groove ball bearings, reduces locomotive damage and maintenance caused by bearing failure, and ensures locomotive operation safety.
c) Results
- Optimized the design and installation of bearings, improving the stability and reliability of operation.
- Improved the overall performance of the motor, reducing downtime caused by bearing failure.
- Reduced equipment maintenance costs and downtime frequency, improving the operational efficiency of locomotives.
- Improved the management and replenishment cycle of grease to ensure lasting lubrication of bearings.
- Reduced the fatigue spalling problem of deep groove ball bearings and improved the service life and safety of equipment.
Customer Testimonials
After using traditional deep groove ball bearings for a period of time, a large number of traction motors were reported for repair and stopped operation. During the bearing maintenance process by the company's technical department, it was found that the bearing surface damage phenomenon was serious. After communicating with QIBR technicians, they provided us with optimized QIBR deep groove ball bearings, reducing the problem of excessive bearing vibration and selecting suitable grease and grease replenishment cycle for the bearings.
The Engineer highly praised QIBR and we will continue to choose QIBR's professional products and services.