QIBR Angular Contact Ball Bearings and Deep Groove Ball Bearings Delivered to London, UK, for Arc Welding Machines to Enhance Safety and Stability
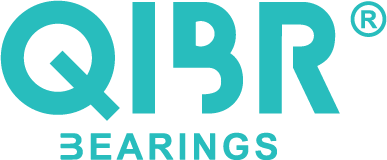
- Continent
- Europe
- Country
- United Kingdom
- Date
- 2016-06-19
- Applications
- Arc Welding Machines
Products Used
Deep Groove Ball Bearing
1. High Load Capacity: The 6040M deep groove ball bearing effectively handles radial loads and some axial loads, with its channel design allowing the steel balls to roll freely, effectively distributing and supporting the loads.
2. Low Friction: Optimized manufacturing processes ensure the geometric shape and dimensional accuracy of the inner and outer rings and rolling elements. Controlled surface roughness and waviness during production reduce vibrations caused by surface defects.
Angular Contact Ball Bearings
1. High Load Capacity: The 7006C angular contact ball bearing can simultaneously support radial and axial loads, with a specific contact angle between the inner and outer rings, increasing axial load capacity and ensuring stable operation under high-load conditions.
2. High Precision: Manufactured to high precision, the 7006C bearing provides stable motion performance, reducing friction and enhancing the efficiency and quality of the welding process.
3. Stability: With high axial stiffness, it minimizes deformation caused by loads, maintaining good performance during high-speed operation, ensuring continuity and stability in the welding process.
Additional Notes:
After evaluating the arc welding machine's requirements for safety and stability, the UK customer decided to procure 7006C angular contact ball bearings and 6040M deep groove ball bearings from QIBR. In the high-load and high-speed environment of arc welding, bearing performance is crucial, directly impacting welding quality and operational reliability. The well-designed 7006C angular contact ball bearing can withstand significant radial and axial loads, while the 6040M deep groove ball bearing offers excellent load capacity and wear resistance. QIBR bearings undergo rigorous testing and certification to ensure stable operation under harsh working conditions. They are manufactured using high-performance materials and advanced processing techniques, providing superior wear resistance and low friction characteristics.