QIBR Slewing Bearings Delivered to Customer in Delhi, India for Aerospace Gyroscopes to Enhance Precision and Durability
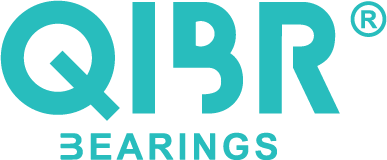
- Continent
- Asia
- Country
- India
- Date
- 2016-05-16
- Categories
-
Slewing Bearing
- Applications
- Aerospace,Gyroscopes
Products Used
Slewing bearing
1. High Precision Positioning: The EB2.25.0475.200-1RPPN slewing bearing features an involute gear design that minimizes side clearance and maximizes meshing accuracy. This ensures tighter contact between gears during rotation, enhancing positioning precision and repeatability, which is critical for the accuracy of gyroscopes.
2. Strong Load Capacity: With a large contact area, the EB2.25.0475.200-1RPPN slewing bearing distributes loads evenly across the entire contact surface. This increased contact area reduces pressure per unit area and improves the bearing's load capacity, allowing it to support loads from multiple directions, including radial, axial, and moment loads, thereby stabilizing rotating components in gyroscopes.
3. Low Friction: The EB2.25.0475.200-1RPPN slewing bearing is manufactured with high precision to ensure geometric and dimensional accuracy. Strict control over machining tolerances and surface roughness minimizes the friction coefficient. The smooth surface reduces contact resistance, ensuring reliable measurement data.
Additional Notes:
The customer in India opted to purchase QIBR's EB2.25.0475.200-1RPPN slewing bearing to meet the demands of their aerospace gyroscopes for enhanced precision and durability. QIBR's EB2.25.0475.200-1RPPN slewing bearing employs advanced manufacturing processes that guarantee extremely high rotational precision while being capable of handling significant radial and axial loads, making it suitable for operation under high-load conditions. This ensures stability and reliability of gyroscopes in complex environments, which is particularly important in aerospace applications where accurate information is required under extreme conditions. The low friction coefficient effectively resists external interference and deformation, ensuring precise positioning of gyroscopes in dynamic environments.